Laminated safety glass holds two layers of glass with an interlayer in the middle,
which prevents pieces from shattering even when damaged.
Laminated safety glass must have an interlayer within it. UVLAM is an interlayer like this, that requires heat, humidity,
and chemicals. A characteristic of UVLAM is that it is highly resistant to heat and humidity, which confirms its capability for environments like shower booths, soundproof walls, construction interior/exterior glasses, and so on.
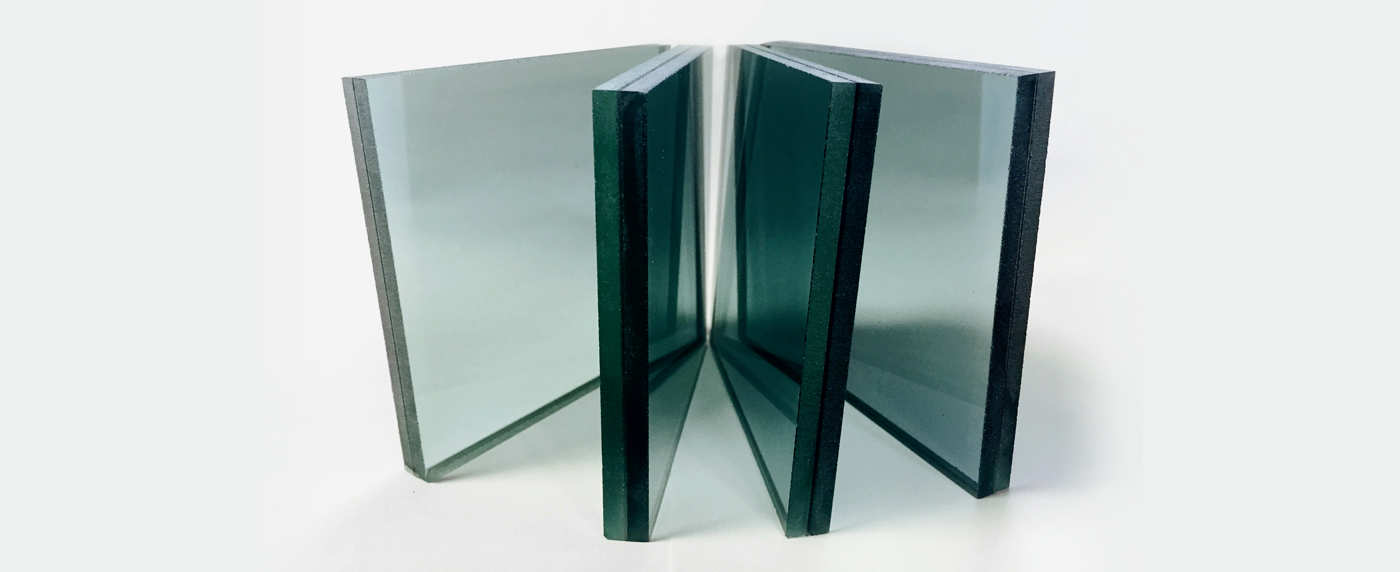
Product Specifications
Comparison between PVB and UVLAM
Why UVLAM?
-
Efficiency in Production Energy Usage
While 500Kwh of energy is required to produce PVB, UVLAM uses 50Kwh
to produce high energy efficiency. it is 90% efficient energy in production line.
Low-carbon manufacturing innovation can be achieved. -
Minimal Machinery & Reduced Risk
In the case of PVB, the size of equipment such as vacuum equipment is large and the risk is very high in case of an accident.
The patented resin injector can produce high-quality, high-accuracy laminated glass. -
Bubbles
On the other hand, UVLAM with low viscosity below 70 cps does not require special high-temperature and high-pressure processes
As the viscosity is low, it fills the unevenness or warpage of the glass surface without any gaps, so there are no bubbles.
Therefore, UVLAM removes air bubbles, which is one of the important factors that cause defects in the durability of laminated safety glass, and thus shows stronger durability compared to glass using PVB, thereby preventing secondary injuries. -
High Clarity
Resin laminated glass with a high refreshing feel is highly favored by customers. Low turbidity (0.7%) of the resin itself maintains low turbidity (0.7%) with bubble-free state even after the process.
-
High temperature stability
Air bubbles are not generated in an environment of 150˚C enabling the wider application of resin.
-
Comparison Viscosity
-
Rough Surface of Tempered Glass